Ardagh Group Cuts Administrative Time In 4
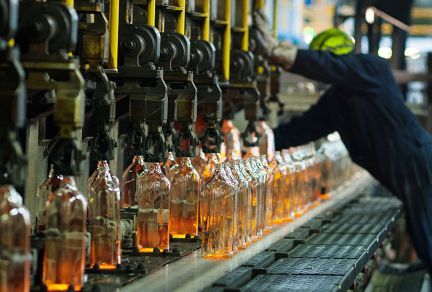
Ardagh, as a global entity, has had a Lean Six Sigma program in place for the past 21 years. Among this, a 5S deployment which involves monthly audits. The average time that they were spending on these audits was at least 10 people per plant spending 2-3 hours to go through all the audits. Because it was mainly Excel-based, it was not standardised across the plants or regions, let alone worldwide. People were going with just a printout of the Excel, walking around the plants while taking pictures with their camera and making notes, then going back to their desks and spending hours to document what they’d found. Let’s do the math.
10 people x 56 plants x 2,5 hours x 12 months = 16.800 hours per year.
That's quite the time commitment. What happened was a divide between the plants who were very structured on the one hand and the less structured ones on the other. Neither was ideal. The ones who respected the instruction were doing it but losing a lot of time and the ones who didn’t were just slowly slipping further. Most of the audits were not being performed or badly documented. What we wanted was to get rid of the administrative time and have more direct activity on the floor to get all of this information, in the right way.
Pierre Autret, LSS director at Ardagh, visited the plant in Dongen 2 or 3 years ago. That’s when he first came in touch with Capptions. His colleague, Ron Prijn, showed him the way they were performing audits and what they were starting to implement. Ron is the Lean Six Sigma Black belt at Ardagh Glass in Dongen. The two of them completed a Capption together on the tablet. That’s when Pierre saw the benefits and how quickly they were able to complete it, first hand. That’s when he had the idea to implement it for all the plants. Ron helped him to develop and sell that to his direct team so they could roll it out to the rest of the plants.
Ardagh had a vision that everyone will be a process improver, every day. And by everyone, they mean everyone, not just management. If you look at all the Lean Six Sigma sides, Pierre says they have done a tremendous job and most of the management is 100% on-boarded, educated, trained and certified. Pierre saw Capptions as the first tool to engage everyone in continuous improvement. This way everyone is involved in the improvement of the plant, me as much as my boss and everyone can record information. The reason we decided to do business with Capptions is that they understood this vision and what we wanted to achieve.
“I like the fact that you are still a young company and you are just doing a great job of listening to your customer. I see that you have lots of potential to adapt to the exact need that we have instead of having a very rigid product that we need to adapt to, instead.”
If we look at the plant that initially piloted the app, in Dongen. Pierre says it’s already amazing to see the difference now versus two years ago. A report of the past 3 months shows that more than 600 audits have been completed. This really shows that the philosophy that he was talking about, that everyone is going to be engaged, it’s happening in these plants. This plant is at the level where he hopes everyone will be soon.
Here in the US the company also saw the opportunity to consolidate all the different audits that were being done in Excel. They now have what they call the master audits, where they take all their EHS, Lean Six Sigma, but also their waste walks and use Capptions for these audits. For this plant, the audits are being done 10 times faster.
“[Capptions] is such a success for me and the fact that every country is starting right now, it’s great.”
Pierre never wanted to force the solution on the plants, instead, he says he’s experiencing a pull. Plants are actively asking for licenses and want to start using Capptions. He sees it being used on a global scale in the near future.
Administration time is the biggest area of improvement for Ardagh Group so far, which has been cut by 4. Pierre visits a plant every other week and has been able to use the app every time. He says it took him 4 times longer in the past, now the report is generated automatically, it’s nice and informal; you can walk around with your phone, talk to your site manager and add pictures. When you’re done you have a complete report that you can share with everyone, which was taking him hours to do before or it wasn’t even being done due to a lack of time. This and the engagement of the people, so they can feel part of the team and use the app for that, those are the 2 main areas that have improved since Ardagh started using Capptions.
“If you’re still doing paper audits, just start using Capptions tomorrow because you’re going to cut your administrative time by four. You’re going to engage your people much more, it’s much more fun to answer a survey on a phone than on a piece of paper. I will highly recommend the app to any new user for sure.”
The ROI from using Capptions was never formally calculated but Pierre says that if they compare it to some of the other software they use, it’s already positive. The time that is being saved can be used for something else that is a benefit for the business. If any of the plants ask for licenses, I would gladly give it to them because I know the value of it and I’m sure that they will still be using it 2 months from now. That can’t be said for all of the software that’s being used within Ardagh. I believe that Capptions is helping us closer towards our vision by allowing anyone to come into the plant, submit suggestions and receive feedback on their suggestions.