OSHA Compliance Checklist: Ensuring Workplace Safety and Legal Adherence
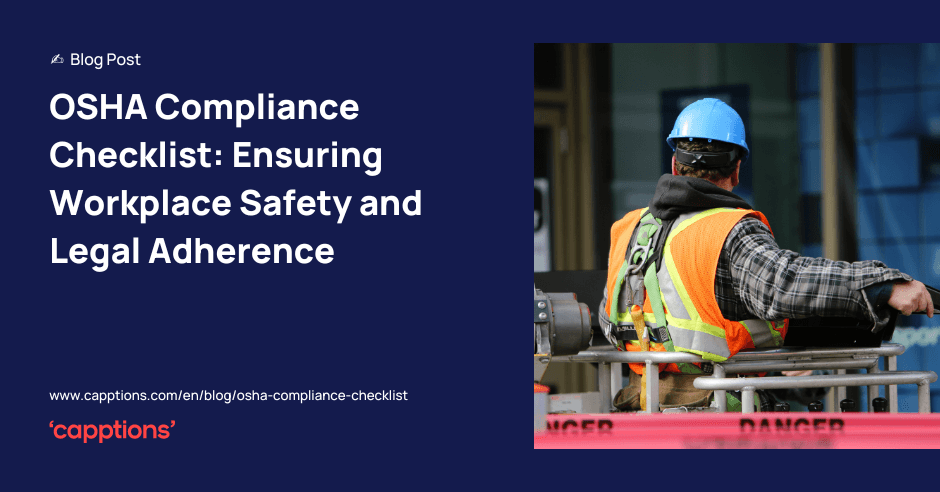
Welcome to our comprehensive documentation on OSHA Compliance Checklist. As a safety and compliance expert, we recognize the critical importance of adhering to Occupational Safety and Health Administration (OSHA) regulations to maintain a safe and compliant workplace. This documentation aims to provide beginners with a detailed understanding of OSHA compliance and equip them with the knowledge and tools necessary to ensure workplace safety and legal adherence. By following the guidelines and best practices outlined in this checklist, organizations can create a safer working environment for their employees and avoid potential penalties or liabilities associated with non-compliance.
1. What is OSHA Compliance Checklist
The OSHA Compliance Checklist is a comprehensive tool that helps organizations assess their compliance with OSHA regulations. It consists of a series of checks and evaluations to identify potential hazards, ensure the implementation of safety measures, and verify compliance with OSHA standards. The checklist covers various aspects of workplace safety, including hazard communication, personal protective equipment (PPE), electrical safety, machine guarding, and more. By following the OSHA Compliance Checklist, organizations can proactively address safety concerns and maintain a safe working environment for their employees.
2. Types of OSHA Compliance Checklist
There are different types of OSHA Compliance Checklists tailored to specific industries and workplace conditions. Some common types include:
- General Industry Checklist: This checklist is applicable to a wide range of industries and covers general safety regulations that apply to most workplaces.
- Construction Industry Checklist: Designed specifically for construction sites, this checklist focuses on hazards and regulations specific to the construction industry, such as fall protection, scaffolding, and excavation safety.
- Healthcare Industry Checklist: Targeting healthcare facilities, this checklist addresses unique safety considerations in hospitals, clinics, and medical offices, including bloodborne pathogens, chemical handling, and ergonomic practices.
- Manufacturing Industry Checklist: Tailored for manufacturing facilities, this checklist emphasizes safety protocols related to machinery, hazardous materials, lockout/tagout procedures, and more.
These are just a few examples, and it's essential to select the appropriate checklist that aligns with your industry and workplace requirements.
3. Why is OSHA Compliance Important
OSHA compliance is of paramount importance as it ensures the health, safety, and well-being of employees in the workplace. Here are some key reasons why OSHA compliance should be a top priority for organizations:
- Employee Safety: Compliance with OSHA regulations helps prevent workplace accidents, injuries, and fatalities. It promotes a culture of safety and protects employees from potential hazards, such as falls, exposure to harmful substances, and electrical incidents.
- Legal Compliance: OSHA regulations are enforceable by law, and failure to comply can lead to severe penalties, fines, and legal liabilities. Compliance demonstrates an organization's commitment to upholding legal requirements and mitigates the risk of legal consequences.
- Reputation and Trust: Prioritizing workplace safety through OSHA compliance enhances an organization's reputation and instills trust among employees, customers, and stakeholders. It demonstrates a commitment to providing a safe working environment and can positively impact employee morale, productivity, and recruitment efforts.
- Cost Savings: Implementing OSHA compliance measures can lead to cost savings in the long run. By preventing workplace accidents and injuries, organizations avoid medical expenses, workers' compensation claims, downtime, and potential lawsuits, resulting in improved financial stability.
Maintaining OSHA compliance is not only a legal obligation but also a moral responsibility that promotes a safe and healthy work environment for everyone involved.
4. Benefits of OSHA Compliance
Complying with OSHA regulations and implementing an effective OSHA Compliance Checklist brings several benefits to organizations:
- Enhanced Workplace Safety: OSHA compliance measures help identify and address potential hazards, reducing the risk of accidents, injuries, and illnesses in the workplace. This creates a safer working environment for employees, promoting their well-being and productivity.
- Legal Protection: By adhering to OSHA standards, organizations protect themselves from legal penalties, fines, and lawsuits. Compliance demonstrates a commitment to following regulations and reduces the likelihood of facing legal consequences.
- Improved Employee Morale: When employees feel safe and confident in their workplace, their morale and job satisfaction increase. OSHA compliance fosters a positive work culture that values employee well-being, leading to higher motivation, engagement, and retention rates.
- Cost Reduction: Preventing workplace accidents and injuries through OSHA compliance can result in significant cost savings. Organizations avoid expenses related to medical treatment, workers' compensation claims, equipment damage, and potential legal fees, contributing to improved financial performance.
- Competitive Advantage: OSHA compliance is often a requirement for participating in certain contracts, tenders, or industry certifications. By demonstrating compliance, organizations gain a competitive edge, opening up opportunities for new partnerships, customers, and business growth.
5. Who is Responsible for OSHA Compliance
OSHA compliance is a shared responsibility among employers, managers, supervisors, and employees. While ultimate accountability lies with the employer, creating a culture of safety and ensuring compliance involves the active participation and commitment of everyone in the organization. Employers are responsible for providing necessary resources, training, and implementing safety programs, while employees must follow established protocols, report hazards, and actively engage in maintaining a safe work environment.
6. How to Conduct OSHA Compliance Inspections
Conducting OSHA compliance inspections involves a systematic approach to identify potential hazards, evaluate current safety measures, and ensure compliance. Here are key steps to conduct effective inspections:
- Prepare: Familiarize yourself with relevant OSHA standards applicable to your industry. Review previous inspection reports, incident records, and safety policies to identify areas of focus.
- Establish a Checklist: Create a comprehensive checklist tailored to your workplace, covering various safety aspects such as equipment, machinery, electrical systems, fire prevention, PPE, and more.
- Schedule Inspections: Plan regular inspections to evaluate compliance. Assign trained personnel or engage external safety professionals to conduct thorough inspections.
- Conduct Inspections: Walk through the workplace, systematically examining equipment, processes, and work areas. Use the checklist to document observations, note potential hazards, and assess the effectiveness of safety measures.
- Identify Corrective Actions: If non-compliance or hazards are identified, prioritize corrective actions and develop a plan to address them promptly. Assign responsibilities and set deadlines for resolution.
- Documentation and Reporting: Maintain detailed records of inspection findings, corrective actions, and completion dates. File reports as required by OSHA regulations.
- Continuous Improvement: Regularly review and update your OSHA Compliance Checklist and inspection processes to reflect changes in regulations, industry best practices, and organizational needs.
By following these steps, organizations can proactively identify and mitigate safety risks, ensuring compliance with OSHA regulations.
7. The Goal of OSHA Compliance
The primary goal of OSHA compliance is to create a safe and healthy work environment for employees. Compliance aims to prevent workplace accidents, injuries, and illnesses by identifying and addressing potential hazards, promoting safety awareness, and enforcing industry-specific regulations. Ultimately, the goal is to protect the well-being and lives of workers while maintaining legal compliance and fostering a culture of safety within organizations.
8. Frequency of OSHA Compliance Checklists
The frequency of conducting OSHA Compliance Checklists depends on various factors such as the nature of the work, industry regulations, and organizational policies. Generally, OSHA compliance checklists should be conducted regularly to ensure ongoing safety and adherence to standards. Key factors to consider when determining the frequency include:
- Regulatory Requirements: Some industries have specific regulations that outline the frequency of inspections or compliance assessments. Ensure compliance with any mandated timelines.
- Work Environment: Assess the level of risk and the changing nature of the work environment. High-risk industries or workplaces with dynamic conditions may require more frequent inspections.
- Incident History: Review past incidents, accidents, near misses, and any changes in work processes to identify patterns or emerging risks that may necessitate more frequent inspections.
- Internal Policies: Consider internal policies and guidelines that may dictate the frequency of inspections. It is crucial to align with organizational safety goals and procedures.
In general, organizations should conduct OSHA Compliance Checklists at least annually, but more frequent assessments may be necessary based on the factors mentioned above. Regular inspections help identify potential hazards, ensure ongoing compliance, and maintain a safe work environment.
9. How to Prepare for an OSHA Compliance Checklist
To prepare for an OSHA Compliance Checklist, organizations should follow these steps:
- Review OSHA Standards: Familiarize yourself with the relevant OSHA standards applicable to your industry. Understand the requirements and specific regulations that pertain to your workplace.
- Assess Current Compliance: Evaluate your organization's current compliance status by conducting a self-assessment. Identify any gaps or areas that need improvement.
- Establish Procedures: Develop procedures and protocols to address areas of non-compliance or improvement. Clearly define responsibilities, roles, and actions required to achieve and maintain compliance.
- Provide Training: Train employees on OSHA standards, safety protocols, and the importance of compliance. Ensure employees are aware of their rights and responsibilities regarding safety in the workplace.
- Implement Safety Measures: Implement necessary safety measures, such as providing personal protective equipment (PPE), maintaining equipment and machinery, conducting regular inspections, and establishing emergency response plans.
- Documentation: Maintain detailed records of training, inspections, incident reports, corrective actions, and any other documentation required by OSHA regulations.
- Regular Review: Continuously monitor and review compliance efforts to ensure ongoing adherence to OSHA standards. Stay updated on changes to regulations and adjust procedures accordingly.
Proper preparation is key to successful OSHA Compliance Checklists, helping organizations identify and address areas of non-compliance, promote a culture of safety, and mitigate risks.
10. Factors That Determine OSHA Compliance Approval or Failure
Several factors contribute to the approval or failure of OSHA compliance. These include:
- Adherence to OSHA Standards: Organizations must demonstrate strict adherence to OSHA regulations and standards relevant to their industry. Failure to comply with specific requirements can result in non-compliance and potential penalties.
- Implementation of Safety Programs: Effective implementation of safety programs, policies, and procedures is essential. Organizations should have documented safety protocols, regular training sessions, and robust safety management systems in place.
- Hazard Identification and Mitigation: The ability to identify potential hazards and take proactive measures to mitigate risks is crucial. Organizations must conduct regular risk assessments, inspections, and promptly address identified hazards.
- Employee Involvement: Active involvement and participation of employees in maintaining a safe work environment are vital. Organizations should encourage employees to report safety concerns, participate in safety training, and follow established safety protocols.
- Documentation and Record-Keeping: Accurate and comprehensive documentation of safety measures, training, inspections, incidents, and corrective actions is necessary to demonstrate compliance and track progress over time.
Organizations that effectively address these factors and prioritize workplace safety are more likely to receive OSHA compliance approval.
11. Understanding OSHA Compliance Reports
OSHA compliance reports provide valuable insights into an organization's compliance status and areas that require attention. These reports may include:
- Inspection Findings: Details of observed hazards, violations, and non-compliance during the inspection process.
- Corrective Actions: Recommendations or requirements for addressing identified hazards or violations. These actions may include deadlines for resolution.
- Citations and Penalties: If serious violations are found, OSHA may issue citations and propose penalties. The report may outline these citations and associated penalties.
- Compliance Recommendations: Suggestions for improving overall compliance and enhancing workplace safety.
- Follow-up Requirements: In some cases, OSHA may require follow-up inspections or verification of corrective actions to ensure compliance.
Understanding and analyzing OSHA compliance reports is essential for organizations to take appropriate action, implement necessary improvements, and maintain a culture of safety.
12. Best Practices for OSHA Compliance Checklists
When conducting OSHA Compliance Checklists, following these best practices can help organizations maximize their effectiveness:
- Regular Training: Provide comprehensive training to employees on OSHA standards, workplace hazards, and safety procedures. Ensure employees are aware of their rights and responsibilities.
- Engage Employees: Foster employee engagement in safety initiatives by encouraging them to report hazards, participate in safety committees, and provide feedback on safety measures.
- Continuous Improvement: Regularly assess and update safety protocols, procedures, and training programs to align with changing regulations, industry best practices, and organizational needs.
- Documentation: Maintain accurate and up-to-date records of safety training, inspections, incidents, and corrective actions. Proper documentation demonstrates compliance and serves as a reference for future improvements.
- Conduct Internal Audits: Periodically conduct internal audits to evaluate compliance, identify areas for improvement, and implement corrective actions.
- Seek Expert Guidance: Engage safety professionals or consultants to provide guidance on compliance, conduct inspections, and offer recommendations for enhancing safety practices.
- Stay Informed: Stay updated on OSHA regulations, industry trends, and best practices through relevant publications, seminars, and training sessions.
By adopting these best practices, organizations can strengthen their OSHA compliance efforts and create a safer work environment for employees.
Conclusion
Maintaining OSHA compliance is crucial for organizations to ensure workplace safety, legal compliance, and the well-being of employees. This comprehensive documentation has provided an in-depth understanding of OSHA compliance checklists, including the definition, types, importance, benefits, responsible parties, implementation process, goals, frequency, preparation steps, approval factors, understanding reports, best practices, and more. By following these guidelines and integrating OSHA compliance into daily operations, organizations can create a culture of safety, prevent accidents and injuries, and foster a productive work environment that prioritizes employee well-being.
To streamline your OSHA compliance efforts and enhance safety management, consider using Capptions' EHS software.