Construction Risk Assessment Checklist
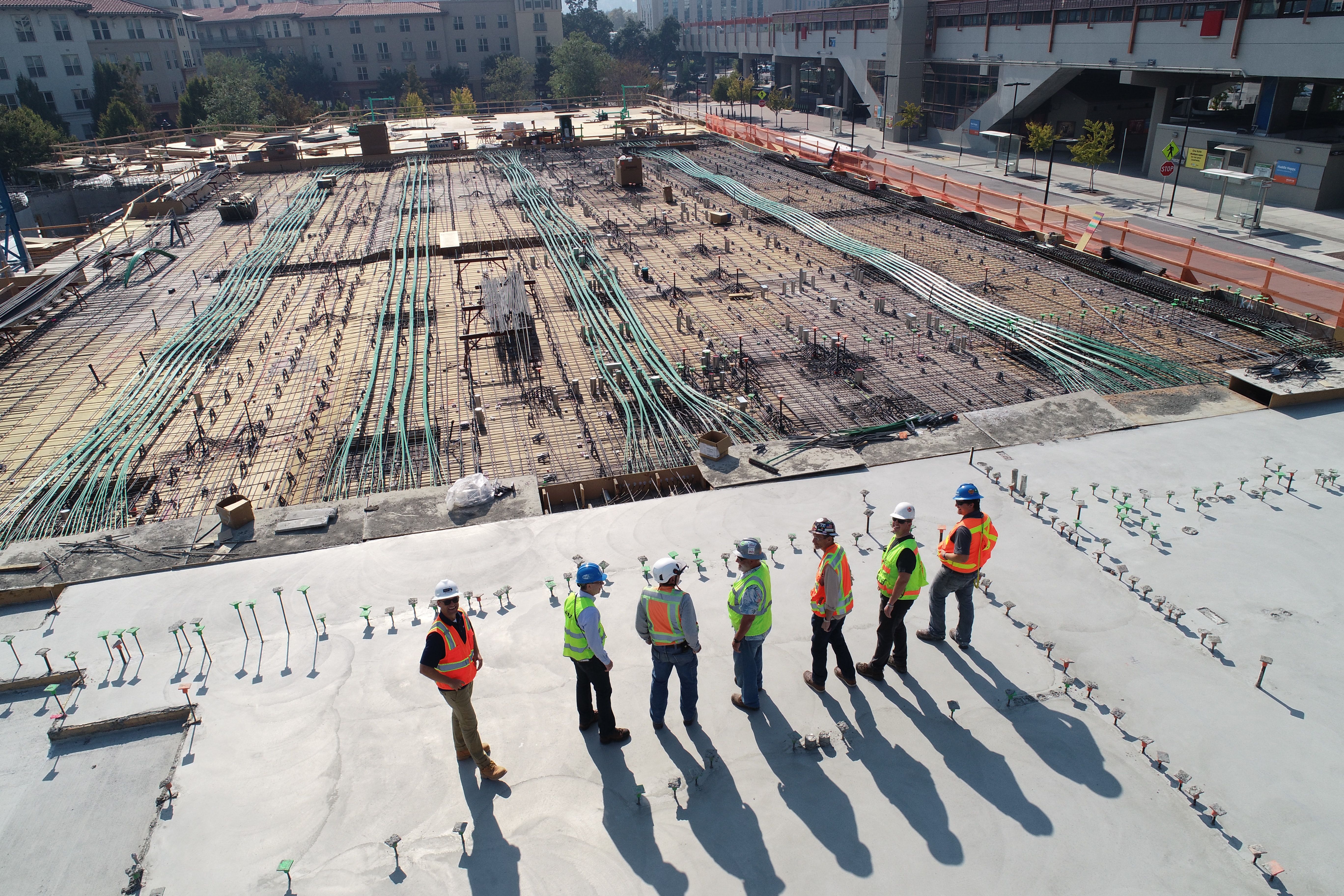
Construction Risk Assessment Checklist
Construction is one of the most dangerous industries in America, with an injury rate more than four times higher than any other industry.
The Occupational Safety and Health Administration (OSHA) reports that every year, construction sites send about 8 million people to hospitals or doctor’s offices for injuries. Of those injured workers, nearly 2 million are treated at emergency rooms for non-fatal injuries which could have been prevented by following safety procedures.
Construction Risk Assessment Checklist offers a comprehensive toolkit to help site managers reduce risk on their sites and prevent accidents from happening. This blog covers everything from scaffolding to forklifts, so you can be sure your whole crew is safe on-site!
The Construction Industry
The construction industry is the construction of buildings, bridges, roads, tunnels, and other large construction projects. The construction industry typically relies on construction management to complete construction projects.
The construction manager ensures that the project is completed on time and within budget constraints. One of his main responsibilities is to coordinate the logistics for construction sites.
Being one of the most dangerous industries to work in, combined with construction companies’ reluctance to make changes to create a safer construction site, means workers are at high risk for illness and injury.
Six out of ten workers experience injuries every year, and construction sites have the highest injury rates among all industries.
It doesn't matter if you're a worker, company manager, company owner, construction company employee - this is an industry that can cause serious injury or death.
Risks in Construction Project
Any project is fraught with risks that can be broadly classified into two categories: those that are associated with the construction process itself, and those that may arise from the use of the completed facility.
Some of the risks that are associated with the construction process itself are related to weather, such as rain, wind, or lightning.
Risks related to conditions, such as uneven ground or unstable soil; and related to the use of equipment, such as power tools or heavy machinery.
Risks that may arise from the use of the completed facility include fire, slips and falls, and injuries caused by contact with hazardous materials.
Occupational Safety and Health Administration (OSHA)
OSHA is the federal agency responsible for ensuring safe and healthful working conditions in the United States. It has the authority to set standards, issue regulations, provide training, conduct inspections, and assess fines for violations of standards or regulations.
The agency was created in 1971, following the passage of the Occupational Safety and Health Act (OSHA). The act gave OSHA authority to set and enforce standards for workplace safety and health. Its goal is to reduce work-related injuries, illnesses, and fatalities.
The agency has a staff of approximately 2,000 inspectors who are responsible for inspecting more than 8 million workplaces. In the fiscal year 2016, OSHA issued more than 83,000 citations and proposed penalties totaling $2.8 billion.
OSHA has a number of programs that are designed to help employers achieve compliance with its standards and more additional resources in order to explain the corrective actions.
These programs include education and training, voluntary consensus standards, cooperative programs, consultation services, and enforcement tools to determine or identify common causes to eliminate incidents and the best practices
Safety Precautions
To reduce the chance of serious harm or death, safety measures are essential in this sector. Safety precautions, such as safety checklists, are needed to ensure workers are not harmed on construction.
There are many different precautions that construction managers should establish. Usually, a list with some of these different types of details should be in the job sites to inform the workers of the multiple risks of their project.
These can include the following points:
- Treat all power tools and machinery with the respect they deserve. This means not using them in an unsafe way, or when you are tired.
- Wear the correct personal protective equipment for the task you are doing. This includes hard hats, gloves, and steel-toe boots.
- Be proactive about safety at the job sites. Do not wait until a worker has been badly injured or killed to fix a problem.
Safety Precautions
Safety Equipment
Construction safety equipment includes all of the things that construction managers have to protect their crew from injury. It could include hard hats, work boots, gloves, etc. However, it also includes more serious construction safety supplies such as respirators, hearing protection, etc.
The construction manager should have construction safety equipment on hand and available for workers. It should be checked periodically for proper care and maintenance.
Respirators
Respirators are important for workers in construction because of the many airborne particles that they can be exposed to. Dust, fumes, and other particles can be dangerous if inhaled. A respirator helps protect the worker from these dangers. There are many different types of respirators, so the construction manager should make sure that he or she chooses the right type for the specific project.
Hearing Protection
Construction workers are often around loud machinery and tools. This can cause long-term damage to their hearing if they are not wearing hearing protection. Hearing protection comes in a variety of forms, including earplugs and earmuffs. The construction manager should make sure that all construction workers are wearing appropriate hearing protection while working.
Hard Hats and Safety Glasses
Hard hats and safety glasses are important for protection from head injuries and eye damage. The construction manager should make sure that all workers on the project at least wear a hard hat when they are in an area where their heads could be impacted (even if there is no danger of falling objects).
Safety glasses help protect eyes from flying debris, such as rocks or metal shavings. They also help protect the eyes from chemical splashes. Both hard hats and safety glasses should be checked regularly for signs of damage so that they will remain effective in protecting the wearer if needed.
Construction Boots
Owning sturdy work boots can keep you safe while working on a construction site, but making sure you always have them on is just as important. Steel-toe boots are crucial for protecting your toes from impact or falling objects, especially when working with heavy tools. Rigid ankle support and good tread work to prevent sprains.
Some jobs require workers to wear safety shoes all the time, but even if you can get away with steel-toed boots only occasionally, it's a good idea to have them with you on-site whenever possible. You never know what job will pop up next! Having multiple pairs of work boots is also an easy way to accommodate different dress codes at different sites.
What is a Risk Assessment Checklist?
A construction risk assessment is an analysis of what might go wrong, and how to avoid it or mitigate its effects.
This involves looking at the probability of something happening, the severity of the potential impact if it does happen, and who would be affected by that event. For example, a chemical company might perform a construction risk assessment on their manufacturing process before changes are made to see what could go wrong.
This includes assessing any issues with processing new chemicals in terms of safety for workers, environmental impacts from chemical leaks or spills, economic damage due to lost production time if accidents do occur, etc.
A more comprehensive assessment can also consider whether adequate training has been provided for staff operating machinery or equipment near hazardous areas ("is there enough space around tanks where they run gas pipes?", "Are operators fully aware of emergency stop procedures?")
A risk assessment checklist helps to ensure that all potential risks are considered before any changes are made. It can also be used as a tool to track progress and ensure that all hazards have been identified and addressed.
A list of questions that should be answered in order to assess the risks associated with a particular task, event, or activity. The questions can vary depending on the type of risk being assessed, but typically they will cover the following topics:
- what could go wrong (identifying)
- what would be the consequences if it did go wrong (severity)
- who would be affected (impact)
What are the five 5 categories of risk construction?
The five categories of risk construction are project, site, products or materials, people, and environment. When risks are associated with the construction process itself, they can be classified as either internal or external risk factors.
Internal factors generally come from direct contact with the construction site such as atmosphere risks which could include asbestos buildup in certain buildings. On the other hand, external risk factors can include hazardous weather conditions like storms which could cause damages to structures on the project.
Therefore when considering these two things it is important that you inspect for these risks during the pre-construction phase where possible because once construction has begun then cost will rise exponentially to try and fix any damage done by poor planning.
How do you write a construction risk assessment?
One of the most important factors in formulating the risks is how much damage can be done to people or property. There are some risks that cause more destruction than others, like earthquakes (which also kill people) and tornadoes (which don't). The scale of threats can make something like children mowing lawns seem far less dangerous than construction.
Before rating potential risks, it's necessary to write them down on paper, once you start rating, you tend not to continue with all items on your list. It's also very helpful if the person rating knows the site. It is easier to describe what's happening right there, rather than relying 100% on someone else's description or uncertain memories.
What are the 5 elements to be considered in a risk assessment?
To be considered in a risk assessment, there are five elements to consider: the environment, health and safety, risks related to other people or property, risks related to the hazards themselves, and finally who are primarily responsible for carrying out risk management activities.
1) Environment: Considering the external environment is something that needs to be done before looking at anything else. What type of weather does this site experience? Is it any extreme temperatures? Any specific geographical conditions that might affect workers' safety? The general environmental conditions need considering.
2) Health & Safety: The number one priority for anyone who carries out any type of work-related activity should be worker health and safety. Whether it’s construction or mining or working alone somewhere outside their office, safety should always be the number one consideration.
3) Risks to Other People or Property: This element can be broken down into two parts: people and property. When looking at risks to other people, employers need to think about things like slips, trips, and falls (especially if there is a risk of injury), contact with hazardous substances, manual handling injuries, etc. With risks to property, it might be thinking about fires, explosions, theft, damage to equipment or vehicles.
4) Hazards themselves: This includes both physical and chemical hazards. It’s important that employees are aware of any potential hazards they may face when carrying out their work tasks.
5) Primary Responsibility for Carrying Out Risk Management: This is probably the most important element to consider when carrying out a risk assessment. Employers need to identify who is primarily responsible for carrying out risk management activities and put together a plan for how those activities will be carried out.
Conclusion
It’s important to be aware of all the risks that come with construction projects. One way to do this is by taking a look at our marketplace. This checklist will help you understand how your company can mitigate or avoid risk in your future projects.
You could also use these guidelines as a template for creating guidelines for individual contractors on your team who are expected to follow them before starting any work on site.
Reviewing this checklist should give you an idea about what areas need improvement if they haven't been addressed already!