EHS Insights: 8 Tips and Tricks to Keeping Your Workplace Safe
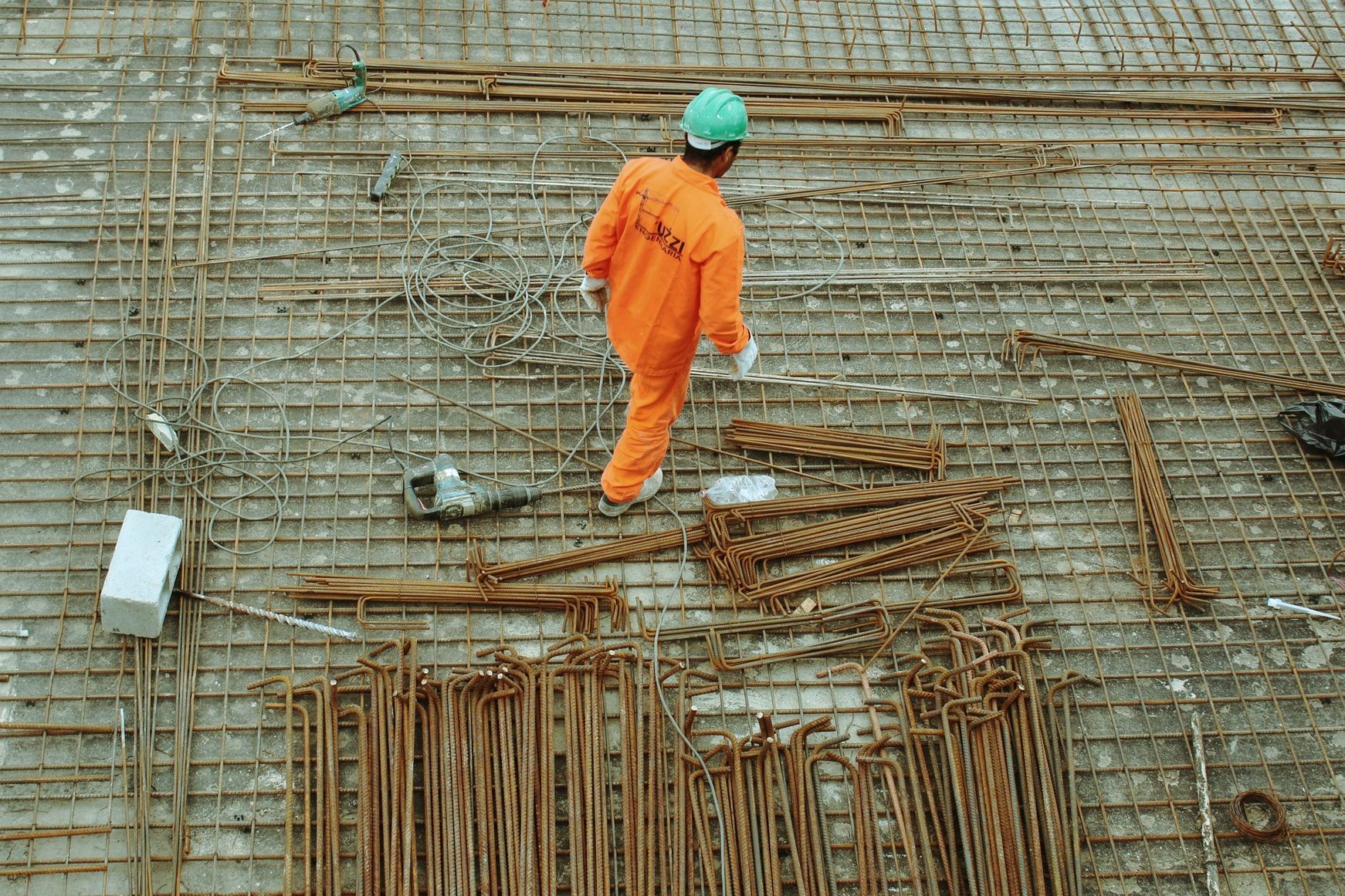
What is the goal of EHS?
The goal of EHS is to protect employees, customers, and the general public from exposure to workplace hazards. EHS professionals work to identify and control these hazards through a variety of methods, including engineering controls, administrative controls, and personal protective equipment. By implementing these controls, EHS professionals can help reduce the risk of injury, illness, and death in the workplace.
One of the most important things you can do to keep your workplace safe is to stay up-to-date on all the latest safety regulations. You can do this by subscribing to safety newsletters or attending safety seminars. Additionally, you should make sure that all of your employees are properly trained on how to safely perform their job duties.
Finally, it's also a good idea to conduct regular safety audits of your workplace. By taking these precautions, you can help ensure that your workplace is a safe and healthy environment for everyone.
What is EHS framework?
An EHS framework is a set of guidelines that helps an organization to manage its environmental, health, and safety risks. It provides a structure for identifying, assessing, and controlling these risks. EHS frameworks can be developed internally by an organization or they can be based on external standards, such as the Occupational Safety and Health Administration's (OSHA) Voluntary Protection Programs (VPP).
When developing an EHS framework, it is important to consider the specific needs of your organization. You should also include input from employees, managers, and other stakeholders. By doing this, you can ensure that your EHS framework is comprehensive and effective.
What are EHS processes?
EHS processes are the procedures and policies that an organization puts in place to manage its environmental, health, and safety risks. These processes can be divided into three main categories: administrative controls, engineering controls, and personal protective equipment.
Administrative controls are procedures that help to minimize exposure to hazards by controlling how work is performed. For example, an administrative control might require employees to wear proper personal protective equipment when working with hazardous materials.
Engineering controls are physical changes made to the workplace that reduce or eliminate exposure to hazards. For example, installing ventilation systems can help to remove harmful fumes from the air.
Personal protective equipment is clothing or devices worn by workers to protect them from exposure to hazards. This might include items such as gloves, safety glasses, or respirators.
By implementing EHS processes, organizations can help to protect their employees from exposure to workplace hazards. These processes can also help to improve the overall health and safety of the workplace.
EHS Training Management
EHS training management is the process of designing, delivering, and evaluating training programs that teach employees about safety hazards and how to protect themselves from exposure. EHS training can be delivered in a variety of formats, including classroom instruction, online courses, and on-the-job training.
When designing an EHS training program, it is important to consider the specific needs of your organization. You should also include input from employees, managers, and other stakeholders. By doing this, you can ensure that your EHS training program is comprehensive and effective.
Evaluating the effectiveness of EHS training is essential to ensure that employees are adequately prepared to protect themselves from exposure to workplace hazards. Evaluation methods can include pre- and post-tests, surveys, and focus groups.
By implementing EHS training management practices, organizations can help to protect their employees from exposure to workplace hazards. These practices can also help to improve the overall health and safety of the workplace.
EHS Software
EHS software is a tool that helps organizations to manage their environmental, health, and safety risks. EHS software can be used to track and report on safety hazards, as well as to develop and implement EHS processes.
When choosing EHS software, it is important to consider the specific needs of your organization. You should also include input from employees, managers, and other stakeholders. By doing this, you can ensure that your EHS software is comprehensive and effective.
There are a variety of EHS software products on the market, so it is important to compare features and prices before making a purchase. Some things you might want to consider include the ability to track safety hazards, create reports, and develop EHS processes.
By implementing EHS software, organizations can help to protect their employees from exposure to workplace hazards. These processes can also help to improve the overall health and safety of the workplace.
Environmental, Health, and Safety
Environmental, Health, and Safety (EHS) is a term that refers to the processes and procedures that an organization puts in place to manage its environmental, health, and safety risks. These processes can be divided into three main categories: administrative controls, engineering controls, and personal protective equipment.
Administrative controls are procedures that help to minimize exposure to hazards by controlling how work is performed. For example, an administrative control might require employees to wear proper personal protective equipment when working with hazardous materials.
Engineering controls are physical changes made to the workplace that reduce or eliminate exposure to hazards. For example, installing ventilation systems can help to remove harmful fumes from the air.
Personal protective equipment is clothing or devices worn by workers to protect them from exposure to hazards. This might include items such as gloves, safety glasses, or respirators.
What does EHS mean in HR?
EHS is responsible for ensuring that workplaces are safe and healthy environments for employees. EHS professionals work to identify and control workplace hazards through a variety of methods, including engineering controls, administrative controls, and personal protective equipment.
EHS is an important part of HR because it helps to ensure that employees are safe and healthy. By taking measures to control workplace hazards, EHS can help to reduce the risk of injury, illness, and death in the workplace. Additionally, EHS can help to improve the overall health and safety of the workplace.
EHS Insight to Keeping Your Workplace Safe
The following are ten tips to help you keep your workplace safe:
- Tip 1: Regularly review your safety procedures and make sure they are up to date.
- Tip 2: Make sure all employees are aware of the procedures and know-how to follow them. Inspect your workplace regularly for hazards and correct any that you find.
- Tip 3: Keep a good stock of safety equipment on hands, such as first aid supplies, fire extinguishers, and Personal Protective Equipment (PPE).
- Tip 4: Train your employees in basic safety procedures, such as first aid and evacuation procedures.
- Tip 5: Investigate any accidents or near-misses that occur in the workplace so that you can learn from them and prevent them from happening again.
- Tip 6: Encourage your employees to report any unsafe conditions or practices that they see.
- Tip 7: Hold regular safety meetings to discuss any concerns and brainstorm ways to improve safety in the workplace.
- Tip 8: Make sure your employees know how to reach you or other designated people if they have any safety concerns.
By following these tips, you can contribute to creating a safe workplace environment for everyone involved. If you have any questions or need further guidance on occupational safety, don't hesitate to reach out to your local EHS Services for expert assistance.
Looking to enhance your workplace safety measures? Consider exploring solutions like Capptions for comprehensive EHS management. Sign up today to ensure your workplace adheres to the highest safety standards.