An Introduction to the Gemba Walk: What it is and How to Do it Right
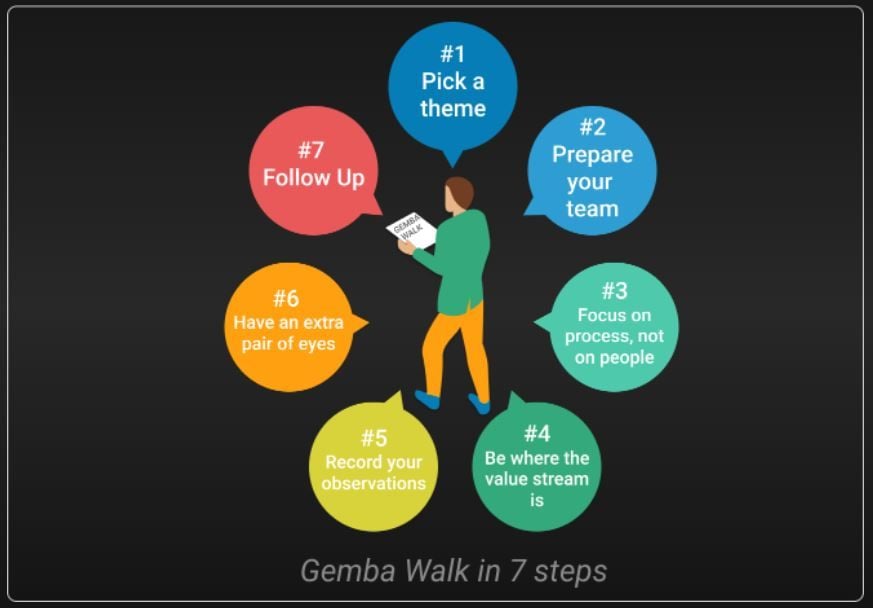
The term “Gemba Walk” may sound foreign, but it’s actually a simple concept. In short, a Gemba Walk is an observational tool used in safety management. It allows you to observe what’s actually happening in your workplace and give you an opportunity to identify any potential safety hazards or issues before they become major problems. Let’s take a closer look at what the Gemba Walk is and how to do it properly.
What does Gemba stand for?
Gemba is a Japanese term that means “the real place”. It refers to the actual location of a process or activity and is used to describe any kind of on-site inspection, observation or walkthrough. The concept was initially developed in Japan in the early 1900s as part of its Total Quality Management movements.
What is a Gemba walk and why is it important?
A Gemba Walk is essentially a walk through your workplace where you observe all of the processes that are taking place on the ground. It’s designed to help you identify any potential safety hazards that could be present in your environment so that you can address them quickly and effectively. During your walk, you should be looking for anything out of the ordinary—including unsafe practices or conditions that could put employees at risk.
Is a Gemba Walks Six Sigma?
Yes, a Gemba Walk is part of the Six Sigma methodology. It is an observational tool that can be used in any industry for safety purposes and to identify potential improvements in your processes.
What is a Six Sigma?
Six Sigma is a set of techniques and tools for process improvement. It focuses on eliminating defects, improving quality and reducing variability in processes to ultimately reduce costs. The goal of Six Sigma is to achieve near-perfection in the processes that you use to make products or deliver services.
Genchi Genbutsu
Genchi Genbutsu is a key component of the Gemba Walk. It's a Japanese term that translates to “go and see for yourself” and it encourages leaders to go out into their workplaces to observe what's happening on the ground. This helps ensure that managers are able to get an accurate picture of how their processes and systems are working, enabling them to make informed decisions about improvements.
Benefits Of A Gemba Walk
The main benefit of a Gemba Walk is that it helps create an open dialogue between management and employees about potential safety concerns in the workplace. This creates an environment of openness and trust while also allowing managers to identify potential problems before they become serious issues. Additionally, by walking through the workplace regularly, managers can ensure that their workers are following proper safety protocols each day.
How To Do A Gemba Walk Properly
When performing a Gemba Walk, there are some key steps that should be followed in order to make sure it is done properly and efficiently. These steps include:
1) Establish Guidelines – Make sure everyone understands their roles during the walk, including who will lead the walk, who will document any findings, etc.
2) Identify Areas Of Concern – Before beginning your walk, take some time to consider any possible areas of concern or areas where safety may be compromised. This will help you know where to focus during your walk so that nothing important goes unnoticed.
3) Document Findings – Once your walk has concluded, document everything that was observed so that corrective actions can be taken if needed.
4) Follow Up – Finally, make sure any recommendations made during your walk are followed up upon with appropriate action items such as implementing preventative measures or providing additional training if necessary.
Gemba Walk Lean
The Gemba Walk is also known as a Lean tool, which means it can be used to identify and eliminate inefficiencies in processes. By walking through the workplace and observing how things are done, managers can pinpoint areas where improvements can be made to streamline operations and reduce waste. This can help save time and money while ensuring that employees are working as safe as possible.
Gemba Walks are an invaluable tool for any organization looking to create a safer work environment, increase efficiency, and ensure quality outputs. By taking the time to observe your processes on the ground, you’ll have a better understanding of how they’re running and what needs improvement so that you can make changes quickly and effectively.
What is a Gemba Visit
A Gemba visit is an on-site investigation that companies often perform to evaluate the current state of their operations. It's a part of Six Sigma and focuses on gathering data from employees, customers, and other stakeholders in order to determine areas for improvement. During a Gemba visit, managers will walk through their operations and observe processes firsthand in order to identify potential issues or opportunities for improvement.
This can include anything from process design, quality control, safety protocols, ergonomics, customer service, etc. Additionally, it allows leaders to engage with their staff in order to get direct feedback which can help them make more informed decisions about any changes they may need to make. With a Gemba visit, organizations are able to stay on top of their operations and ensure that they remain agile, efficient, and effective.
Furthermore, Gemba visits help foster a culture of continuous improvement as it allows for both leaders and employees to take ownership over the development of processes. This helps create an atmosphere of trust and collaboration between staff, which in turn can lead to improved morale and productivity.
Additionally, by engaging with employees directly during a Gemba visit, organizations are able to identify potential issues or opportunities quickly without having to rely on long-term surveys or data collection. Finally, conducting regular Gemba visits helps managers stay up-to-date with how their operations are running in real time rather than relying on outdated information from the past which can cause them to miss out.
How to Continuous Improvement in Your Business
Continuous improvement is an ongoing process that organizations use to continually improve the products and services they offer. It involves identifying areas for improvement, making necessary changes, measuring results, and then repeating the process over again. In order to effectively implement continuous improvement in your business, there are a few steps that you can take:
1) Identify Areas of Improvement – Take time to assess current processes and identify opportunities for improvement.
2) Set Goals & Objectives – Once you’ve identified potential areas of improvement, set goals and objectives so that everyone understands what needs to be accomplished.
3) Implement Changes – Make any changes needed in order to meet the goals and objectives that were set. This may include updating processes, providing additional training, or introducing new technology.
4) Measure Results – Regularly measure the results of the changes in order to determine whether they are having a positive impact on the business.
5) Review & Modify – As needed, review and modify any existing processes or procedures in order to ensure that they remain effective and up-to-date.
6) Use Gemba Walks – Utilize Gemba walks as part of your continuous improvement process in order to get direct feedback from employees and identify potential areas for improvement quickly.
Continuous improvement is an ongoing process that requires dedication and commitment from everyone involved in order to be successful.
What is 5s Management
5s management is a method of workplace organization and standardization that can help businesses create a more efficient and effective workspace. The 5s stands for: Sort, Set in Order, Shine, Standardize and Sustain. By following these five steps, companies can ensure their workspace is organized, clean, safe and free of clutter which can lead to increased productivity.
#1. Sort
This first step involves sorting through all the items in the workspace and getting rid of anything that is unnecessary or not being used regularly. This helps reduce clutter and makes it easier to find what you need when you need it.
#2. Set in Order
Once everything has been sorted out, organize remaining items into easily identifiable categories so they are easy to find when needed.
#3. Shine
Keeping a clean workspace is essential for efficiency and safety. This step involves regularly cleaning the workspace and making sure everything is properly stored away.
#4. Standardize
This step involves creating routines, processes and standards for how work is to be done in order to ensure consistency and accuracy in all tasks.
#5. Sustain
Lastly, sustainment means taking steps to maintain the 5s system by continually monitoring and evaluating procedures to identify areas of improvement.
By following these five steps, businesses can create a better working environment that leads to improved morale, productivity and cost savings.
Conclusion
Completing regular Gemba Walks is essential for maintaining a safe work environment for both employees and employers alike. By keeping an eye out for potential hazards and addressing them quickly, businesses can ensure they are creating a safer space for everyone involved while also avoiding costly citations from regulatory agencies down the line. If done correctly, these walks can provide invaluable insight into how operations are running on-site each day which can then be used to improve processes going forward!