Dock Operations Made Safe: Your Ultimate OSHA Loading Dock Safety Checklist Manual
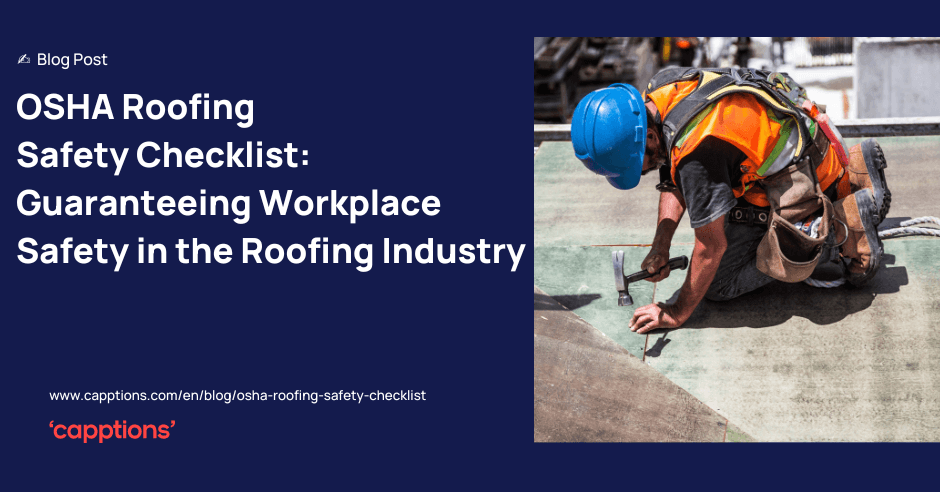
Welcome to our comprehensive guide on OSHA Loading Dock Safety Checklist, where safety and compliance take center stage. As experts in safety and compliance, we understand the critical importance of ensuring a safe and secure environment in loading dock areas. The loading dock is a hub of activity in warehouses and distribution centers, where goods are loaded and unloaded, making it a high-risk area for accidents and potential hazards. The OSHA Loading Dock Safety Checklist serves as a powerful tool to systematically assess and address safety concerns, mitigating risks and promoting a culture of safety in the workplace. In this documentation, we will delve into all aspects of the OSHA Loading Dock Safety Checklist, from its purpose and types to the steps for conducting a thorough inspection and best practices to enhance safety. Let's dive in to equip you with the knowledge and resources to ensure loading dock safety and protect the well-being of your workforce.
1. What is OSHA Loading Dock Safety Checklist
The OSHA Loading Dock Safety Checklist is a comprehensive evaluation tool designed to assess the safety conditions and compliance standards of loading dock areas. Created by the Occupational Safety and Health Administration (OSHA), this checklist serves as a guideline to ensure that loading dock operations adhere to safety regulations, promoting the well-being of workers and preventing accidents or injuries. By implementing this checklist, businesses can identify potential hazards, address safety concerns, and maintain a secure loading dock environment that aligns with OSHA standards.
2. What Are The Types of The OSHA Loading Dock Safety Checklist
The OSHA Loading Dock Safety Checklist can encompass various types of inspections, each catering to specific aspects of loading dock safety. Some common types include:
- General Safety Inspection: A comprehensive assessment covering various safety aspects, such as structural integrity, equipment functionality, and worker practices.
- Fire Safety Inspection: Focused on fire prevention measures, including fire extinguisher accessibility, proper storage of flammable materials, and functional fire alarms.
- Electrical Safety Inspection: Evaluates the electrical systems, wiring, and grounding to prevent electrical hazards and potential shock risks.
- Fall Protection Inspection: Concentrated on fall prevention measures, such as guardrails, safety nets, and harnesses, to safeguard workers from elevated risks.
3. Why is it Important
The OSHA Loading Dock Safety Checklist is of utmost importance for several compelling reasons:
- Worker Safety: Prioritizing loading dock safety through inspections reduces the likelihood of accidents and injuries, protecting the well-being of workers.
- Compliance with Regulations: Adherence to OSHA guidelines and safety standards ensures legal compliance, minimizing the risk of penalties and fines.
- Enhanced Productivity: A safe and well-organized loading dock fosters efficiency and productivity in material handling operations.
- Risk Mitigation: Identifying and addressing potential hazards proactively minimizes risks and potential liabilities for businesses.
4. What are the Benefits of OSHA Loading Dock Safety Checklist
Implementing the OSHA Loading Dock Safety Checklist yields several significant benefits, including:
- Accident Prevention: Identifying and addressing safety concerns in loading dock areas reduces the occurrence of accidents and injuries.
- Cost Savings: Prevention of accidents and injuries leads to reduced worker compensation claims and associated costs.
- Improved Morale: Prioritizing worker safety boosts employee morale and confidence in the workplace.
- Legal Protection: Compliance with OSHA regulations provides legal protection for businesses against potential lawsuits and penalties.
5. Who is responsible to do the OSHA Loading Dock Safety Checklist
The responsibility for conducting the OSHA Loading Dock Safety Checklist typically falls on trained safety officers or designated safety compliance personnel within the organization. These individuals possess the expertise to identify potential hazards and ensure compliance with safety standards.
6. How is the OSHA Loading Dock Safety Checklist Done
The OSHA Loading Dock Safety Checklist involves a systematic approach to assess loading dock safety:
- Comprehensive Inspection: Safety officers conduct a thorough evaluation of the loading dock area, equipment, and safety measures.
- Identification of Hazards: Potential safety hazards, such as slippery surfaces, damaged equipment, or insufficient lighting, are identified.
- Documentation: Inspection findings are documented, including safety violations and recommended corrective actions.
- Rectifying Safety Issues: Necessary measures are taken to address identified safety concerns and hazards promptly.
7. What is the Goal of OSHA Loading Dock Safety Checklist
The primary goal of the OSHA Loading Dock Safety Checklist is to ensure a safe and compliant loading dock environment that prioritizes worker safety and prevents accidents. By identifying potential hazards and addressing safety concerns, businesses create a secure working environment for all loading dock operations.
8. How Often Should You Do a OSHA Loading Dock Safety Checklist
The frequency of conducting the OSHA Loading Dock Safety Checklist may vary based on several factors, including:
- Regulatory Requirements: Compliance with local, state, and federal regulations that mandate specific inspection intervals.
- Nature of Operations: The intensity and frequency of loading dock activities may influence the inspection frequency.
In general, regular inspections are recommended to ensure ongoing safety and compliance.
9. How to Prepare a OSHA Loading Dock Safety Checklist
To prepare for the OSHA Loading Dock Safety Checklist, consider the following steps:
- Designate Inspection Team: Assign trained safety personnel to perform the checklist inspection.
- Review OSHA Guidelines: Familiarize the inspection team with OSHA loading dock safety regulations and guidelines.
- Gather Necessary Tools: Equip the inspection team with appropriate tools, such as safety checklists, measuring instruments, and personal protective equipment (PPE).
- Conduct Pre-Inspection: Perform a preliminary check of the loading dock area to identify visible hazards or issues.
- Coordinate with Stakeholders: Collaborate with warehouse management and loading dock personnel to ensure a smooth inspection process.
10. What Makes a OSHA Loading Dock Safety Checklist Approve or Fail
The OSHA Loading Dock Safety Checklist is considered approved when:
- Compliance with Safety Standards: The loading dock area meets all OSHA safety standards and guidelines.
A OSHA Loading Dock Safety Checklist may be considered failed when:
- Safety Violations Exist: The checklist identifies significant safety violations or hazards that pose immediate risks to workers and loading dock operations.
- Non-Compliance with Regulations: The loading dock fails to meet OSHA safety regulations and guidelines.
11. How to Understand The OSHA Loading Dock Safety Checklist Reports
Understanding OSHA Loading Dock Safety Checklist reports involves:
- Reviewing Findings: Thoroughly reviewing the inspection reports, including identified hazards and recommended corrective actions.
- Prioritizing Corrective Actions: Addressing high-priority safety issues promptly to minimize risks.
- Seeking Professional Guidance: Consulting safety experts or OSHA compliance consultants for expert advice on addressing safety concerns.
12. What Are The Best Practices When Doing a OSHA Loading Dock Safety Checklist
When conducting the OSHA Loading Dock Safety Checklist, adhere to these best practices:
- Thoroughness: Perform a comprehensive and detailed inspection, leaving no potential safety hazards unchecked.
- Communication: Communicate safety inspection findings clearly to all stakeholders, including management and employees.
- Training and Education: Provide training to loading dock personnel on safe practices and emergency procedures.
- Regular Follow-Ups: Schedule regular follow-up inspections to ensure ongoing compliance and safety.
Conclusion
The OSHA Loading Dock Safety Checklist serves as a crucial tool in ensuring the safety and compliance of loading dock areas. By following the checklist guidelines, businesses can create a secure and efficient working environment for all loading dock operations. From preventing accidents and reducing costs to complying with OSHA regulations, the benefits of a comprehensive safety checklist are immense. Let us prioritize the safety of our workforce and loading dock operations to foster a culture of safety and well-being.
For advanced safety management solutions and tools, explore Capptions.